The Importance of Risk Assessment in Contractor Safety Management
- Penelope Harriet
- May 6
- 5 min read
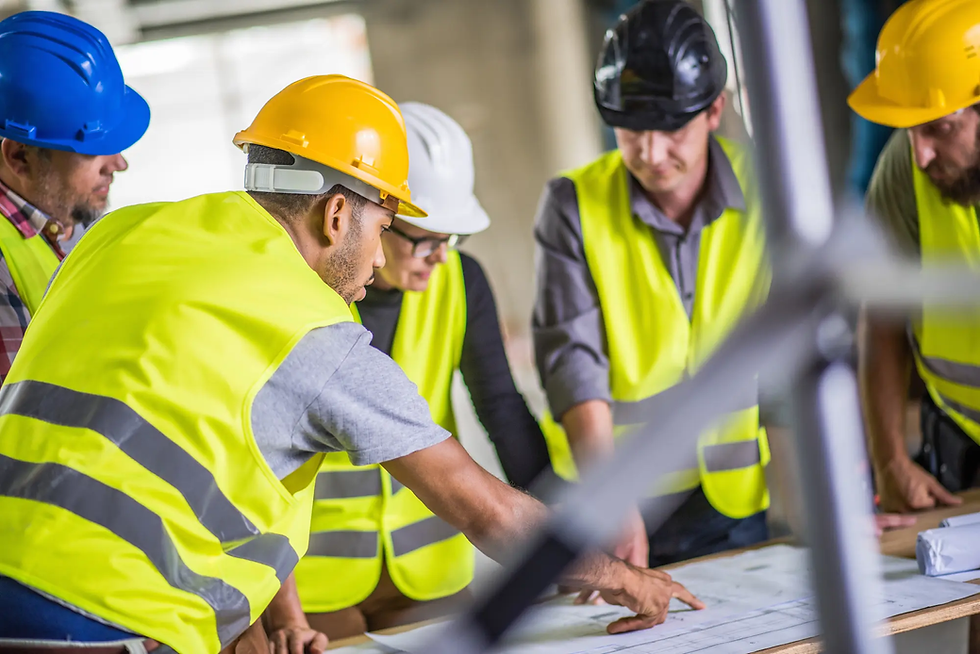
When it comes to workplace safety, managing risks is one of the most crucial responsibilities for any organization, especially when working with contractors. Ensuring that contractors work in a safe environment not only protects them but also minimizes the risk of accidents, damages, and potential legal consequences. Risk assessment in contractor safety management plays an essential role in identifying hazards and taking proactive measures to control or eliminate them. It ensures that contractors follow safe practices while working on a project, ultimately safeguarding everyone involved.
In this article, we’ll dive into the importance of risk assessment in contractor safety management, offering a step-by-step guide on how organizations can effectively manage these risks. We will also discuss how tools like the OSHA 30 Hour Course can play a vital role in enhancing contractor safety awareness.
Why Risk Assessment Matters in Contractor Safety Management
A risk assessment is the first line of defense when it comes to preventing workplace accidents and injuries. It’s a systematic process of identifying hazards, evaluating the risks associated with them, and deciding on appropriate measures to control those risks. In the context of contractor safety, risk assessments are essential because contractors often work in dynamic environments, which may expose them to different safety hazards compared to regular employees.
For example, imagine a construction company hiring a contractor to work on scaffolding. Without a thorough risk assessment, the contractor might not be aware of the specific dangers related to working at heights, such as fall hazards, equipment malfunction, or unsafe weather conditions. The risk assessment will help identify these potential dangers and ensure that the contractor is fully prepared to handle them.
Risk assessment is also important for regulatory compliance. Organizations are legally required to ensure the safety of contractors and employees, and failure to conduct proper risk assessments can lead to hefty fines or lawsuits.
Step-by-Step Guide to Conducting Risk Assessments for Contractors
To ensure that contractors are working safely, organizations must conduct thorough risk assessments. Here’s a step-by-step guide on how to carry out a proper risk assessment for contractor safety management:
Step 1: Identify the Hazards
The first step in the risk assessment process is identifying potential hazards at the workplace. Hazards can vary depending on the nature of the work being done. Common hazards for contractors include:
Physical hazards: such as heavy machinery, scaffolding, and electrical equipment
Chemical hazards: exposure to harmful chemicals like solvents or paints
Environmental hazards: like extreme weather conditions, noise, or poor lighting
Ergonomic hazards: from manual handling, repetitive motions, or awkward postures
A good risk assessment starts by recognizing all potential risks to ensure that the contractor’s work environment is safe. This process involves inspecting the work site, consulting with workers who have experience in the field, and reviewing past accidents or incidents that may have occurred.
Step 2: Evaluate the Risks
Once the hazards are identified, the next step is to assess the risks associated with each hazard. This includes determining how likely an accident or injury is to occur and the severity of the potential consequences. For example, a contractor working on electrical wiring may be at high risk of electrical shock, while a contractor working with power tools may be at risk of cuts or amputations.
This evaluation helps prioritize which risks need immediate attention and which ones can be addressed with less urgency. A risk matrix can be used to plot the likelihood of each hazard occurring against its severity. This matrix will help organizations focus on the most significant risks first.
Step 3: Control the Risks
After evaluating the risks, the next step is to control or eliminate them. There are several ways to manage risks, including:
Eliminating the hazard: If possible, remove the risk altogether (e.g., using a safer tool or method)
Substituting the hazard: Replace a dangerous material or method with a safer alternative
Engineering controls: Implement safety measures like guardrails, barriers, or ventilation systems to prevent accidents
Administrative controls: Establish procedures or policies that reduce risk (e.g., limiting the time contractors spend on high-risk tasks)
Personal protective equipment (PPE): Ensure contractors wear the necessary safety gear, such as helmets, gloves, and safety goggles
Risk control measures must be carefully selected based on the severity and likelihood of the risks involved. For example, in the case of working at heights, scaffolding with proper guardrails or fall arrest systems is essential to prevent serious injuries.
Step 4: Monitor and Review
After implementing control measures, it is crucial to continuously monitor the work site to ensure the safety of contractors. Regular checks and audits will help identify any gaps or issues in the safety measures, allowing for corrective actions to be taken before an accident occurs. It’s also essential to review the risk assessment regularly, especially when there are changes in the work environment or procedures.
How OSHA 30 Hour Course Improves Contractor Safety Awareness
The OSHA 30 Hour Course is a comprehensive training program designed to educate workers about workplace safety, with a particular focus on identifying hazards and understanding the necessary control measures. Contractors who undergo this training are better equipped to recognize potential dangers and take the appropriate steps to mitigate them.
The course covers topics such as:
Fall protection
Electrical safety
Hazardous materials
Personal protective equipment (PPE)
Emergency procedures
By taking the OSHA 30 Hour Course, contractors gain essential knowledge that not only helps them comply with OSHA regulations but also fosters a culture of safety on the job site. This training ensures that contractors understand their responsibilities when it comes to managing risks and maintaining a safe work environment.
Read More about OSHA 30 Hour Training.
Step 5: Ensure Communication and Collaboration
Effective communication is vital when managing contractor safety. All stakeholders, including contractors, site managers, and safety officers, must work together to ensure everyone is aware of potential hazards and how to avoid them. Regular safety meetings and toolbox talks can be useful for maintaining communication about safety protocols.
Contractors should also have a clear understanding of the company’s safety culture and how it aligns with their responsibilities. Encouraging an open dialogue about safety concerns can help identify hazards that might not be immediately obvious.
The Role of Technology in Risk Assessment
In today’s digital age, technology has made conducting risk assessments more efficient and effective. Many organizations now use specialized software to track risks, manage assessments, and monitor safety compliance. These tools allow for better documentation, easier access to safety information, and more streamlined reporting.
One example is using mobile apps to conduct real-time hazard assessments. Contractors can easily record and report any potential hazards they encounter on the job, allowing for immediate corrective actions. Technology also helps organizations track contractor training and ensure that they are up to date with the latest safety requirements.
Conclusion
In conclusion, risk assessment in contractor safety management is not just a legal requirement; it’s a critical practice for protecting contractors and the entire workforce. By following a structured risk assessment process, organizations can identify and control potential hazards, reduce the likelihood of accidents, and maintain a safe working environment for everyone.
Providing contractors with adequate training, such as the OSHA 30 Hour Course, helps ensure they are equipped with the knowledge to manage risks effectively. By investing in training and safety programs, companies show their commitment to safety, which ultimately leads to a more productive, accident-free work environment.
Comments