How to Write Clear and Practical Safe Work Procedures
- Penelope Harriet
- May 10
- 5 min read
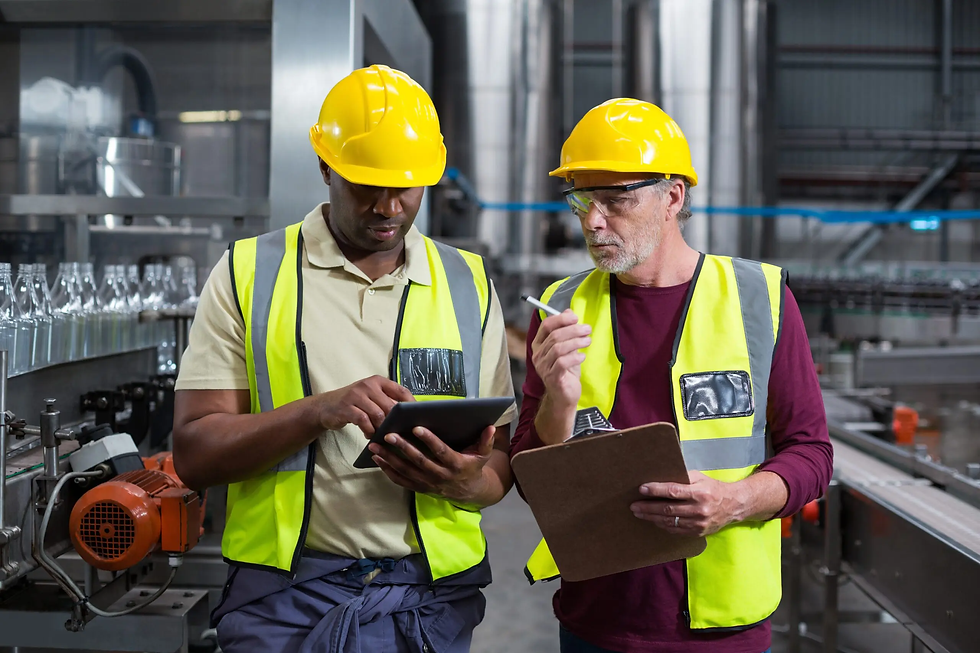
In every workplace—whether it's a factory floor, a construction site, or even an office—safety procedures are more than just checklists. They are the lifeline that keeps workers informed, hazards managed, and incidents minimized. Yet, many organizations overlook one critical element: clarity.
A Safe Work Procedure (SWP) that's confusing or vague is like a map without landmarks—it won't guide anyone safely.
If you're responsible for health and safety in your workplace, or if you're a team leader, supervisor, or safety officer, understanding how to write clear and practical safe work procedures can help you protect lives, save money, and ensure legal compliance.
Let’s break it all down into simple, real-life language and a step-by-step process that you can start using today.
Why Clear Safe Work Procedures Matter
Imagine this: Ahmed, a maintenance technician at a manufacturing plant in Lahore, was assigned to repair a conveyor belt. The procedure document said, “Ensure the equipment is safe to use.” That’s all. No steps, no details. So, Ahmed assumed everything was fine. Moments later, a sudden jolt from the machine almost crushed his hand.
This happened because the Safe Work Procedure wasn’t clear or practical. Unfortunately, stories like this aren’t rare.
Workplace injuries are not only costly—they’re often preventable. This is where structured training like the NEBOSH course in Pakistan comes in. It empowers professionals to recognize workplace hazards, assess risks, and develop sound procedures based on international safety standards.
What Is a Safe Work Procedure (SWP)?
A Safe Work Procedure is a formal, written instruction designed to guide workers on how to perform a task safely and efficiently. It outlines potential workplace hazards, risk control measures, necessary personal protective equipment (PPE), and the correct way to complete a task.
Unlike policy documents that are often high-level, an SWP focuses on "how-to" instructions in plain language.
Step-by-Step Guide to Writing Practical Safe Work Procedures
Let’s get into the core of this guide. Here’s a step-by-step approach to creating a clear and effective SWP.
Step 1: Identify the Task
Start with a specific task. Don't write generic instructions like “operate machinery.” Instead, focus on one task at a time, such as “Changing blades on the paper-cutting machine.”
This prevents misunderstandings and ensures each SWP is tailored.
Step 2: Break It Down Into Steps
Once you have the task, divide it into clear, small steps. Think of it like teaching someone who’s never done the job before. Use bullet points or numbered lists.
For example:
Shut off the power supply.
Lockout/tagout the machine.
Remove the safety guard.
Use wrench to unscrew blade.
Replace blade carefully using gloves.
Each step should answer: What should be done, how should it be done, and what safety precautions are required?
Step 3: Identify Hazards
After outlining the steps, look at each one for possible hazards. This can include:
Sharp tools
Electrical risks
Toxic fumes
Falling objects
You can use a Job Hazard Analysis (JHA) or Risk Assessment tool to help identify risks systematically.
Step 4: Control the Risks
Now that you’ve identified hazards, it’s time to add control measures. This could mean using PPE (like gloves or goggles), installing guards, or changing how the task is done.
For instance, if there's a risk of hand injury, add: “Wear cut-resistant gloves before removing blades.”
Make sure to include emergency procedures in case something goes wrong.
Step 5: Use Clear, Simple Language
This is where most SWPs fail. Use everyday language. Avoid technical jargon unless it’s necessary—and if you must use it, define it.
Don’t write:
“Depress the hydraulic actuator in alignment with the rotational axis.”
Do write:
“Push the lever down to stop the rotating part.”
Use action words like “turn off,” “wear,” “lift,” or “check.” Always write in the active voice.
Step 6: Include Visuals Where Possible
A picture truly is worth a thousand words. Use diagrams, photos, or flowcharts to explain complex steps. Especially in high-risk industries, visuals can be a lifesaver.
Consider marking up images to show where switches are, how guards are positioned, or where warning signs should be placed.
Step 7: Review and Test the Procedure
Don’t just write it and forget it. Take it to the workers who actually do the job. Ask:
Does it make sense to you?
Can you follow it without confusion?
Is anything missing?
Update the procedure based on feedback. It’s a living document—treat it that way.
Step 8: Train Your Team
An SWP is only effective if your team knows it exists and understands it. Conduct training sessions, post procedures near the work area, and review them regularly.
In fact, continuous learning is essential in safety. That’s why enrolling your safety officers in the NEBOSH course in Pakistan is such a smart move—it’s not just about compliance, but building a culture of safety.
Tips to Make Your Safe Work Procedures Even Better
Even a good SWP can be great with a few extra touches:
Use headings and subheadings to organize large documents.
Highlight warnings using bold or color formatting.
Link related documents such as MSDS sheets or equipment manuals.
Add review dates to ensure they stay updated.
Translate documents if you have a multilingual workforce.
Common Mistakes to Avoid
Many workplaces rush through this process. Here are a few pitfalls to watch out for:
Copy-pasting procedures from other jobs or industries.
Using overly technical or vague language.
Not involving the actual workers during creation.
Failing to update SWPs after changes in equipment or process.
Real-World Example: How Clear Procedures Saved the Day
At a garment factory in Faisalabad, a worker named Maria was assigned to clean a thread-cutting machine. Her supervisor gave her a laminated Safe Work Procedure that clearly outlined each step—from shutting off the machine to the correct way of handling cleaning solvents.
Halfway through the job, she noticed a small leak. Thanks to her training, she referred to the “spill response” section of the same procedure, handled it correctly, and reported it. A potential fire hazard was neutralized.
Clarity made all the difference.
Why Invest in Safety Training?
Safety procedures are only as effective as the people implementing them. That’s why formal education plays a huge role. The NEBOSH Safety Course in Pakistan is highly recommended for anyone working in high-risk industries like construction, manufacturing, or oil and gas.
It covers real-world scenarios, teaches legal responsibilities, and equips professionals with the tools to write, evaluate, and enforce clear safety procedures.
Conclusion: Safety Starts with Clarity
Writing clear and practical safe work procedures isn’t just a regulatory requirement—it’s a commitment to your team’s well-being. It sends a message that safety isn’t just lip service. It’s a way of working, thinking, and living.
When you provide clear instructions, involve your workers, and ensure everyone is trained, you do more than prevent accidents—you create a safe, productive, and trusting environment.
Start today. Review one of your workplace procedures using the steps in this guide. If it doesn’t meet the clarity test, revise it.
Because when it comes to workplace safety, clarity saves lives.
Comentários