Don’t Cut Corners! How Faulty Equipment Jeopardizes Workplace Safety
- Penelope Harriet
- Mar 20
- 4 min read
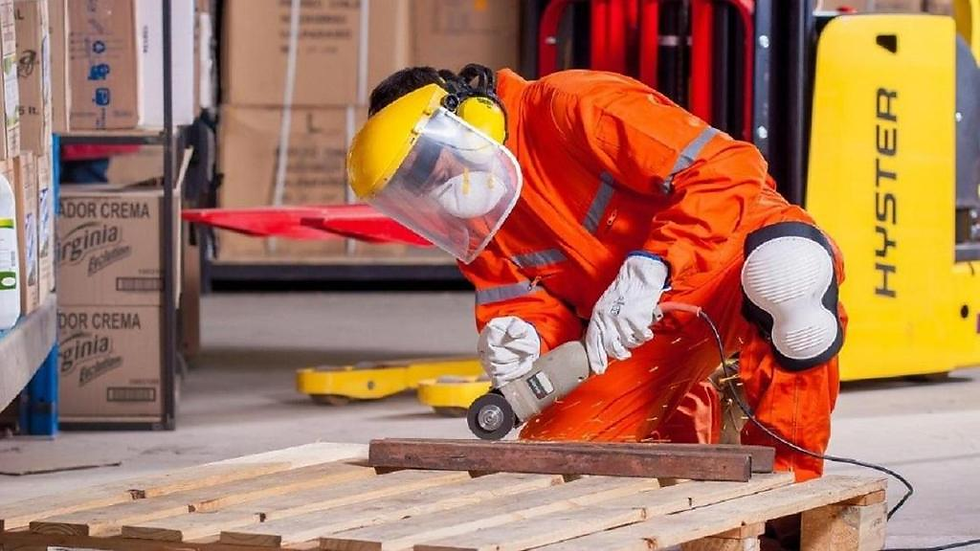
Imagine you’re operating a forklift, and just as you turn a corner, the brakes fail. Or picture a factory worker using a defective drill that suddenly malfunctions. These aren’t just hypothetical scenarios—they are real-life workplace hazards caused by faulty equipment. Every year, thousands of workers suffer injuries due to poorly maintained or defective machinery. The cost isn’t just measured in medical bills but also in lost productivity, legal liabilities, and even lives.
Cutting corners when it comes to workplace safety can have disastrous consequences. Investing in high-quality, well-maintained equipment is crucial for preventing accidents and ensuring smooth operations. This article explores the dangers of using faulty equipment and provides actionable steps to keep your workplace safe.
Read More about the benefits of NEBOSH Course in Pakistan and how it can enhance workplace safety.
Understanding Workplace Hazards Due to Faulty Equipment
Workplace accidents can happen in any industry—from construction sites to offices. However, some of the most severe incidents occur due to malfunctioning or poorly maintained tools and machines. These issues arise due to:
Lack of regular maintenance
Use of outdated or worn-out equipment
Ignoring safety inspections
Failure to train employees on proper usage
Addressing these factors can significantly reduce the risk of injuries and improve workplace efficiency.
The Hidden Dangers of Faulty Equipment
1. Increased Risk of Injuries
When machinery is not properly maintained, the risk of accidents skyrockets. Loose wires, broken gears, or faulty brakes can lead to devastating injuries, including:
Cuts and amputations from defective saws and cutting tools
Electrocution from exposed wires in electrical appliances
Crushing injuries from malfunctioning hydraulic systems
For example, a warehouse worker using a defective conveyor belt could easily get their hand caught, leading to severe injury or even permanent disability.
2. Reduced Productivity and Downtime
When equipment fails unexpectedly, production slows or stops completely. This not only affects deadlines but also results in financial losses. Companies that don’t invest in regular inspections may find themselves dealing with:
Unplanned downtime
Delayed projects
Increased repair costs
3. Legal and Financial Consequences
Employers are legally required to provide a safe working environment. If an accident occurs due to negligence in maintaining equipment, companies can face:
Lawsuits from injured employees
Hefty fines from safety regulatory bodies
Increased insurance premiums
For instance, a manufacturing company that fails to replace a faulty machine part may be held liable for injuries sustained by a worker due to equipment failure.
Step-by-Step Guide to Ensuring Workplace Safety
Step 1: Conduct Regular Equipment Inspections
Preventive maintenance is the key to avoiding accidents. Employers should:
Schedule regular inspections to check for wear and tear
Replace faulty parts before they cause a problem
Keep a record of all maintenance activities
Using checklists can help teams systematically inspect equipment and ensure compliance with safety regulations.
Step 2: Train Employees on Proper Equipment Use
Even the best tools are dangerous if not used correctly. Training should include:
Understanding equipment manuals
Identifying warning signs of malfunction
Knowing emergency shutdown procedures
Employees who complete safety training, such as a NEBOSH Course in Pakistan, are better equipped to handle workplace hazards and prevent accidents.
Step 3: Invest in Quality Equipment
While cutting costs on equipment may seem like a smart financial decision, using cheap, unreliable tools can be disastrous. Investing in high-quality, durable machinery reduces the risk of breakdowns and increases workplace safety.
Step 4: Establish an Emergency Response Plan
Even with precautions, accidents can still happen. Employers must:
Provide workers with first aid training
Install emergency shut-off systems on machinery
Ensure clear communication channels for reporting defects
A well-prepared workforce can significantly reduce the severity of workplace accidents.
Real-Life Example: A Lesson in Workplace Safety
Consider the case of Ali, a construction worker who was using a power drill with a loose handle. Despite reporting the issue, his supervisor insisted on continuing the work. One day, the handle snapped, causing Ali to lose control and injure his hand. The accident resulted in weeks of recovery time and a lawsuit against the company.
This unfortunate incident could have been prevented with timely maintenance and prompt action on reported defects. Ignoring safety concerns is never worth the risk.
How a Safety Courses Can Help
If you want to take workplace safety seriously, enrolling in a NEBOSH in Pakistan is a smart move. NEBOSH courses equip individuals with the knowledge and skills needed to:
Identify and mitigate workplace hazards
Conduct risk assessments effectively
Ensure compliance with health and safety regulations
By investing in safety training, companies can reduce workplace accidents and improve overall productivity.
Conclusion:
Faulty equipment is a ticking time bomb in any workplace. Ignoring maintenance, skipping safety inspections, and failing to train employees properly can lead to severe injuries, financial losses, and legal trouble. Employers must prioritize safety by investing in quality equipment, regular maintenance, and proper training.
If you’re committed to workplace safety, consider enrolling in a NEBOSH Course in Pakistan to gain essential knowledge and ensure a hazard-free work environment. After all, safety isn’t an expense—it’s an investment in your team’s well-being and your business’s success.
Comentários